Electroplating Production Lines
For a number of years, our company has been involved in the production and assembly of complete lines, designed for electroplating metallic materials. The size and number of single electroplating baths and thus the total built-up area depend on the kind and quantity of goods to be electroplated, as well as on the type of finish.
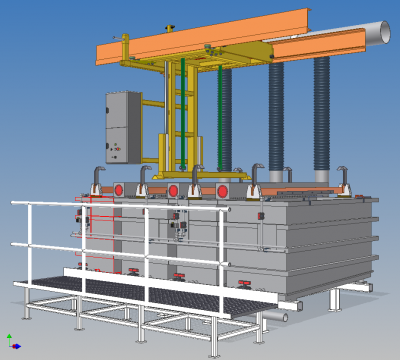
When planning a line, it must be clear what kind of goods is to be electroplated in the line. This is needed to determine the minimum inner dimensions of plating baths, which must be additionally en26px;d if accessories are used, such as heating or plating bath stirring. Our bathtubs are mostly made of polypropylene (PP); this type of bathtub is used most often. The bath consists of a steel base welded of standard parts and PP-wrapped to prevent plating bath chemicals from contacting the steel sections. A PP-made bottom is welded to the base; the bottom is sloped down to the drain, so that the bath can be emptied completely and cleaned. A casing is welded to the bottom; the casing is peripherally reinforced with steel PP-wrapped struts as in the tray shown in the figure below.
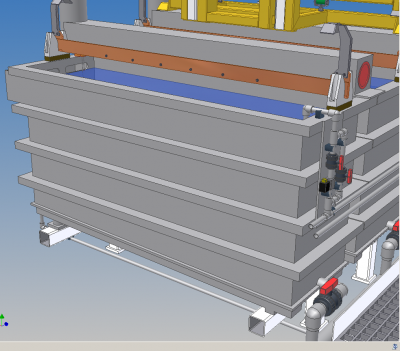
The inner dimensions are decisive for the overall bath size; these are: width (the bathtub dimension in the plane perpendicular to the manipulator travel track), length, and depth. As standard, baths are equipped with PP-made DN 50 ball valves in the drain.
The bath shape depends on the operations to be performed in it. For instance, rinse tubs are equipped with a spillway trap. The polluted water is either drained into the sewage piping, or into a special device, where it is cleaned and pumped back to be reused in the line. The baths we produce may be single-position or multi-position ones; the individual positions in multi-position baths may be separated by partitions. As per the plating process, baths are equipped with accessories. The standard equipment includes, for instance, supporting sockets; electro-conductive sockets; heating or cooling registers; clarification equipment; ejector mixing; temperature and level sensors; automatic bath replenishment; cathode bar mechanical motion; filtration, and others.
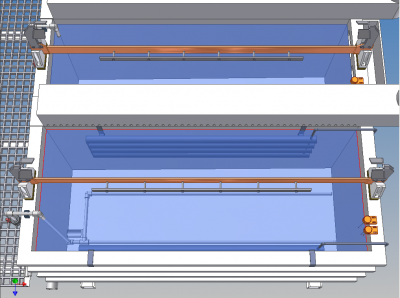
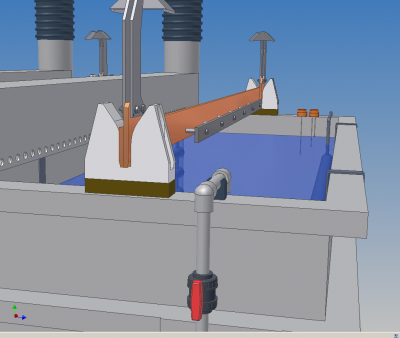
Baths are equipped with both cathode and anode sockets as required by the plating process. Either cathode bars with hanging items, or metal-plating drums are seated in the sockets. Handling of cathode bars or metal-plating drums is carried out exclusively by manipulators; they are divided into two categories: the more common suspended manipulators travelling over the track above the line, as shown in the figure below, fall into the first category.
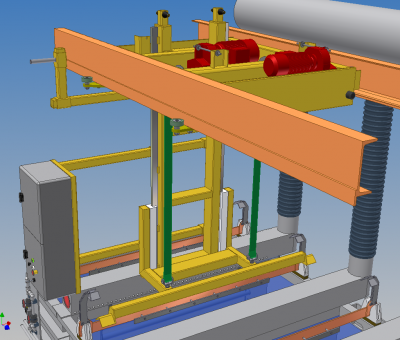
The second category includes portal manipulators travelling over the track along the baths approximately at their upper edge. This solution is more complicated and used only when no suspension manipulators can be used in the production facility. Depending on the program, handling of bars or drums may be performed either automatically, semi-automatically, or manually. Manipulators are equipped with a travel and lifting device to best suit customer requirements.
To exhaust the vapours formed in some baths during the plating process, the line is equipped with an exhaust system as standard. The most common arrangement is shown in the figure.
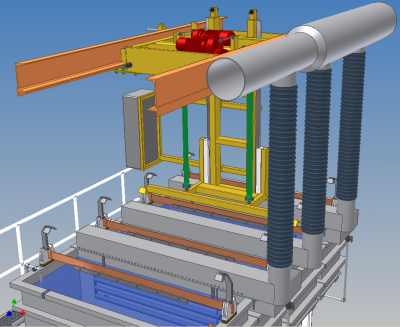
This exhaust system consists of exhaust frames located at the edge of baths where the vapours form. At their sides, the exhaust frames are equipped with orifices that suck the vapours in. There is a plugged opening in the frame's face designed for maintenance.
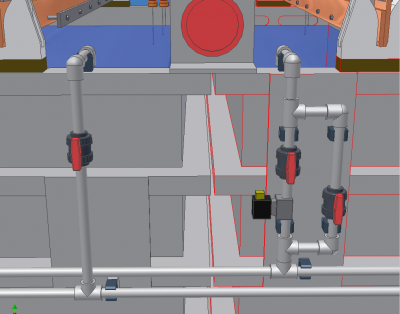
The exhaust frames are connected to a suction manifold via flexible hoses. The blower-driven vapours flow through this manifold and out of the plating shop by vacuum action. An exhaust system built in the baths' side walls close under the edge is the less commonly used variant. It is used in locations where there is a risk of damaging the exhaust frames when handling goods. Such a situation may occur, e.g., when bulky pieces are put in the bath via cranes or other similar lifting devices. Baths may be equipped with closing lids to enhance exhaust efficiency as much as possible.
Most commonly, plating lines are laid on steel structures, as shown in the figure below:
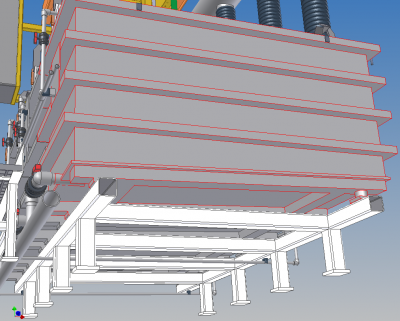
These steel structures allow the baths to be adjusted to the required height and simultaneously the sewage piping to be sufficiently sloped. These structures are made of plain or stainless steel. A PVC film is interlaid between the structure and the bath to prevent bath drops from acting directly on the structure.
There is a service walkway on one side of the line that is equipped with all control elements, such as distribution valves for pressurised air, water, or bath escape valves. The height of this walkway depends on the height of the baths’ upper edge above the floor. The distance of the walkway grille is shown in the figure.
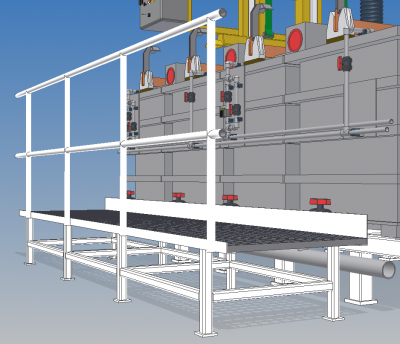
This distance is usually approx. 1,000 mm above the baths’ upper edge, or as required by the customer. The walkway is equipped with a handrail, a gutter bed, and stairs. The most common widths of walkways are 800 or 1,000 mm. The walkway grille may be made of plastics, steel, possibly hot-dip zinc coated.